

金属蚀刻详细介绍
本视频可以帮助朋友们详细了解蚀刻加工的整个流程及工艺控制的大致要点,可以帮助您全面了解金属蚀刻整个控制过程。本质上金属蚀刻一个多流程,多管控的一个操作过程,任何一道工序都可以决定了最终的品质。
金属蚀刻(etching)是将材料使用化学反应或物理撞击作用而移除的技术。金属蚀刻技术可以分为湿蚀刻(wet etching)和干蚀刻(dry etching)两类。金属蚀刻是由一系列复杂的化学过程组成,不同的腐蚀剂对不同金属材料具有不同的腐蚀性能和强度
金属的种类不同,其蚀刻的工艺流程也不同,但大致的工序如下但大致的工序如下:金属蚀刻板→清洁除油→水洗→干燥→贴膜或丝网印刷油墨→干燥→曝光图形→显影→水洗干燥→蚀刻→退膜→干燥→检验→成品包装。
通常所指金属蚀刻也称光化学金属蚀刻(photochemical etching),指通过曝光制版、显影后,将要金属蚀刻区域的保护膜去除,在金属蚀刻时接触化学溶液,达到溶解腐蚀的作用,形成凹凸或者镂空成型的效果。最早可用来制造铜版、锌版等印刷凹凸版,也广泛地被使用于减轻重量(Weight Reduction)仪器镶板,铭牌及传统加工法难以加工之薄形工件等的加工;经过不断改良和工艺设备发展,亦可以用于航空、机械、化学工业中电子薄片零件精密金属蚀刻产品的加工,特别在半导体制程上,金属蚀刻更是不可或缺的技术
金属蚀刻工艺流程
金属的种类不同,其蚀刻的工艺流程也不同,但大致的工序如下:金属蚀刻板→清洁除油→水洗→干燥→贴膜或丝网印刷油墨→干燥→曝光图形→显影→水洗干燥→蚀刻→退膜→干燥→检验→成品包装。
1.金属蚀刻前的清洁工序
在不锈钢或其它金属蚀刻之前的工序都是清洁处理,主要的作用就是清除材料表面的脏污,灰尘,油渍等。这首工序是否很好的完成,是保证贴膜或丝印油墨与金属表面是否具有良好附着力的关键工序,因此必须要彻底清除金属蚀刻表面的油污及氧化膜。除油应根据工件的油污情况定出方案,最好在丝印油墨前进行电解除油,保证除油的效果。除氧化膜也要根据金属的种类及膜厚的情况选用最好的浸蚀液,保证表面清洗干净。在丝网印刷前要干燥,如果有水分,也会影响油墨的附着力,而且影响后续图纹蚀刻的效果甚至走样,影响蚀刻效果。
2.贴干膜或丝印油墨感光胶层
根据实际的产品材质,厚薄以及图形的精密宽度确认采用干膜或湿膜丝印,针对不同的厚薄产品,在涂感光胶层时,要考虑到产品的图形需要的蚀刻加工的时间等因素,以便制得较厚或适用较薄的的感光胶层,这样才使得遮盖性能好,金属蚀刻加工出的图纹清晰度高。
3.干燥
贴膜或滚涂丝印油墨完成后,需要彻底的将感光胶层进行干燥,为曝光工序进行准备工序,同时需要保证表面清洁,无粘连,杂质等。
4.曝光
此工序为金属蚀刻的重要工序,曝光能量的大小会根据产品的材料的厚度,精密精细度来考虑。这也是一个蚀刻加工企业的技术能力的体现。曝光工序决定了蚀刻能否保证有较好的尺寸管控精度等要求。
5.显影
金属蚀刻板的表面感光胶层经过曝光处理后,图形胶层经过光照后固化的金属板上,此后要将图形中不需要的,即要将需要腐蚀掉的部份裸露出来。显影的工序也决定的产品最终尺寸能否达到要求。此工序将产品上覆盖的不需要感光胶层会完全的清除掉。
6.蚀刻或腐蚀工序
最为关键的工序,产品前制工序完成后。会进行进行化学药液的蚀刻。此过程决定了最终产品是否合格的关键工序。整个过程涉及到了蚀刻药水的浓度,温度,压力,速度等参数,产品的质量均需要由这些参数共同决定。
7.退膜
蚀刻后的产品,表面仍覆盖着一层感光胶层覆盖着。这道工序需要将蚀刻加工完后的产品表面的感光胶层进去退膜去除。由于感光胶层是酸性物质,因此绝大多数均采用酸碱中和法进行膨松,溢流水洗加超声波清洁后,除去表面的感光胶层。本工序主要防止有感光胶的残留。
8.退膜完成后,剩下的就是检查,包装。尺寸的检查保证不能有任何不良品流出到客户手上。
减少侧蚀和突沿,提高金属蚀刻加工系数
侧蚀产生突沿。通常印制板在金属蚀刻液中的时间越长,(或者使用老式的左右摇摆蚀刻机)侧蚀越严重。侧蚀严重影响印制导线的精度,严重侧蚀将使制作精细导线成为不可能。当侧蚀和突沿降低时,蚀刻系数就升高,高的蚀刻系数表示有保持细导线的能力,使蚀刻后的导线接近原图尺寸。电镀蚀刻抗蚀剂无论是锡-铅合金,锡,锡-镍合金或镍,突沿过度都会造成导线短路。因为突沿容易断裂下来,在导线的两点之间形成电的桥接。
提高板子与板子之间蚀刻加工速率的一致性
在连续的板子蚀刻中,金属蚀刻加工速率越一致,越能获得均匀蚀刻的板子。要达到这一要求,必须保证蚀刻液在蚀刻的全过程始终保持在最佳的蚀刻状态。这就要求选择容易再生和补偿,蚀刻速率容易控制的蚀刻液。选用能提供恒定的操作条件和对各种溶液参数能自动控制的工艺和设备。通过控制溶铜量,PH值,溶液的浓度,温度,溶液流量的均匀性(喷淋系统或喷嘴以及喷嘴的摆动)等来实现。
提高整个板子表面金属蚀刻加工速率的均匀性
板子上下两面以及板面上各个部位的蚀刻均匀性是由板子表面受到金属蚀刻剂流量的均匀性决定的。蚀刻过程中,上下板面的蚀刻速率往往不一致。一般来说,下板面的蚀刻速率高于上板面。因为上板面有溶液的堆积,减弱了蚀刻反应的进行。可以通过调整上下喷嘴的喷啉压力来解决上下板面蚀刻不均的现象。蚀刻印制板的一个普遍问题是在相同时间里使全部板面都蚀刻干净是很难做到的,板子边缘比板子中心部位蚀刻的快。采用喷淋系统并使喷嘴摆动是一个有效的措施。更进一步的改善可以通过使板中心和板边缘处的喷淋压力不同,板前沿和板后端间歇金属蚀刻蚀刻的办法,达到整个板面的蚀刻均匀性。
金属蚀刻加工的一些共性特点说明
关于开模及费用: 相对低廉的开模费用,普通的情况下200-1000元不等(特殊的玻璃光罩会贵一些)。更新设计的时间快,最快可一天内即可完成设计的更新并完成模版制作,且成本较小。
新产品的开发周期:针对金属蚀刻加工工艺的新产品开发可以更灵活,费用低。设计人员在新品开发时,可以提前和我们沟通,这样可以经过双方的讨论,来规避一些设计上的缺陷。比如:设计的材料厚度,设计的加工管控精度,可以蚀刻的最小孔,最小的缝隙等。可以提前将设计图发至邮箱:ly@sz-ydf.com进行前置讨论。或电话联系:刘生135 3425 7051
金属蚀刻加工可实现的一些特殊作用:金属蚀刻加工可以实现冲压,切割或CNC达不到的凹凸效果:比如一些LOGO,品牌标识等,且立体感强,图案任意,精细度高
金属蚀刻加工通用的一些可管控精度:依据材料材质,厚度,本厂加工精度大约可以换算成材料厚度的10%,比如0.1mm厚的不锈钢,可管控的精度为+/-0.01mm
金属蚀刻可加工的一些形状:几乎可以任意形状。依据材料厚度的不同,形状可开的最小开孔会有所不同,越厚的板子,可开的形状间隙需要越大。复杂外形的产品同样可以蚀刻,无需额外增加成本。
金属蚀刻可加工一些材料厚度:最为理想状态是:0.05mm-0.5mm厚度区间。目前本厂可加工材料厚度控制在0.02mm-2.0mm。越厚的板材需要蚀刻加工的时间会更久,相对成本会更高。同时,超薄的材料加工成本也不会低,过程管控防变形等操作需要特殊对待。
蚀刻加工可以加工一些材质:理论上,所有的金属材料均可以被腐蚀或蚀刻加工。只是针对不同的材料会采用不同的化学配方,抗腐蚀性能好的材料比如金,银等甚至需要王水型蚀刻配方才能蚀刻。考虑到风险因素及量产性,本厂绝大部份采用SUS304,SUS316不锈钢蚀刻加工,以及所有的铜材,铜合金,钼片类材料均可以蚀刻。
蚀刻加工特别优点:由于金属蚀刻加工是通化学药水的方式进行浸蚀。
1.最为显著的优点就是产品跟原材料保持高度一致。不改变材料的性状,不改变材料应力(除表面半蚀刻的以外),不改材料的硬度,拉伸强度及屈服强度及延展性。基加工过程在设备中是经过雾化的状态进行蚀刻,表面无明显压力。
2.没有毛剌:产品加工过程,全程无冲压力,因此不会产生卷边,突点,压点。
3.可以和后工序冲压配合完成产品的单独成型动作,可以有挂点的方式进行整版电镀,背胶,电泳,黑化等,相对成本更为节省。设计挂点方式可以联系刘先生:ly@sz-ydf.com;135 3425 7051
4.小型化,多样化同样可以应对,且周期短,成本小。这就为国内外一些小型或独角兽型的公司提供一更好的解决方案,用我们的专门的样品制样组,达到快速交期的目的,同时产品质量又能得以保证。
金属蚀刻加工的连接点设计方式
金属蚀刻加工厚度对应的连接大小设计参考
|
||||
厚度mm
|
内凹设计(形成产品缺口)
|
外凸设计(形成产品边缘毛剌)
|
||
蚀进深度
|
蚀进宽度
|
凸出高度
|
凸出宽度
|
|
0.10
|
0.15
|
0.60
|
0.05-0.15
|
0.12-0.15
|
0.15
|
0.2
|
0.75
|
0.05-0.15
|
0.12-0.15
|
0.20
|
0.25
|
0.90
|
0.05-0.15
|
0.12-0.15
|
0.25
|
0.3
|
0.90
|
0.20
|
0.12-0.15
|
0.30
|
0.35
|
1.00
|
0.20
|
0.2
|
0.40
|
0.4
|
1.30
|
0.20
|
0.3
|
0.50
|
0.4
|
1.50
|
0.30
|
0.4
|
0.60
|
0.4
|
1.60
|
0.36
|
0.4
|
0.70
|
0.4
|
1.65
|
0.30
|
0.5
|
0.80
|
0.45
|
2.40
|
0.40
|
0.5
|
1.00
|
0.45
|
2.50
|
0.40
|
0.5
|
备注:所示单位均为mm单位
化学蚀刻溶液配方及工艺条件
蚀刻不同的金属要采用不同的溶液配方及工艺条件,常用金属材料的蚀刻溶液配方及工艺条件见表6—4~表6-6。
表6-4金属化学蚀刻溶液的配方及工艺条件
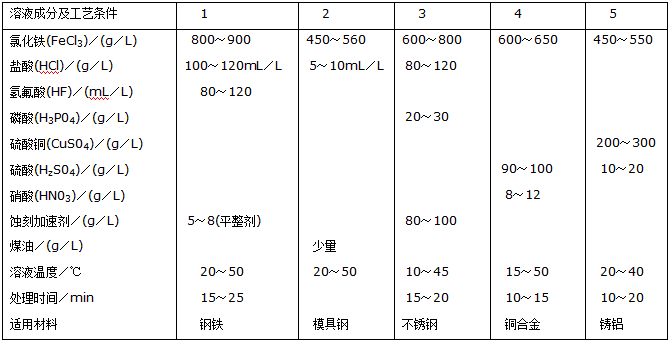
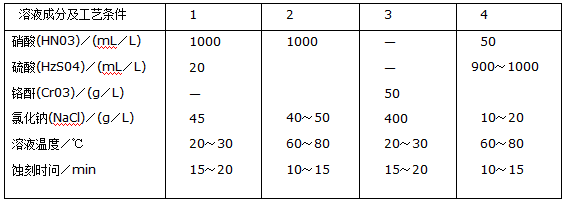
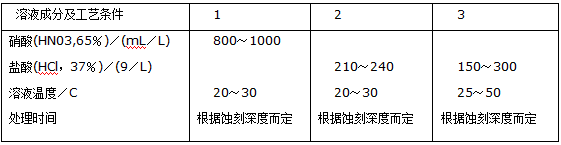
工艺操作条件的影响
蚀刻是金属板模图纹装饰过程中的关键,要想得到条纹清晰、装饰性很强的图纹制品,必须注意控制好蚀刻工艺的条件。主要是蚀刻溶液的温度和蚀刻时间。溶液温度稍高,可以提高金属溶解的速度,也就是蚀刻的速度,缩短蚀刻所需要的时间,但是蚀刻溶液一般都是强酸液,强酸液在温度高的情况下腐蚀性强,容易使防护的涂层或耐蚀油墨软化甚至溶解,使金属非蚀刻部位的耐蚀层附着力下降,导致在蚀刻和非蚀刻交界处的耐蚀涂层脱落或溶化,使蚀刻图纹模糊走样,影响图纹的美观真实和装饰效果,因此温度不宜超过45℃。 同样,如果蚀刻的时间太长,特别是蚀刻液温度较高的情况下,耐蚀油墨或防护涂层浸渍时间过长,也同样起到上述的副作用和不良后果,因此时间控制上也要适当,不能浸得太久,一般不宜超过20~25min。
FeCl3 金属蚀刻原理的发现
Fecl3金属蚀刻是最早使用的一·种用于铜及台金蚀刻的加工方法,这种方法,原料容易获得,价格便宜,配制简单,易于操作,因此这一方法曾经被广泛采用,即便是现在也被较多的铜蚀刻厂所采用。但这种方法对环境污染较重而被其他的腐蚀方法所逐渐取代。
Fecl,对铜的腐蚀是一个氧化还原过程,在铜表面Fe3+铜氧化成Cucl3同时Fe3被还原成Fe3+
FeCl3蝕刻原理的介绍:
(1)FeCL3浓度对蚀刻速度的影响:FeCL3蚀刻液中随着FeCL3浓度的增高,蚀刻速度加快。当所含FeCL3超过某一浓度时,由于溶液黏度增加,蚀刻速度反而有所下降。
(2)盐酸的添加量对蚀刻速度的影响:在蚀刻液中加入盐酸,一则可以抑制FeCL3和CuCL2的水解;二则可提高蚀刻速度。特别是当蚀刻液中铜含量达到37.4g/L后,盐酸的作用更加明显。
(3)温度对蚀刻速度的影响:在FeCL3蚀刻工艺中,随温度的增加,蚀刻速度亦加快,比如当温度在50度时,全新蚀刻液对铜的蚀刻速度可达10um/min。但在实际生产中,都是采用常温蚀刻方法。FeCL3对铜的蚀刻是一个放热反应,随着蚀刻的进行,蚀刻液温度会逐渐升高,蚀刻速度加快。随着FeCL3的消耗,蚀刻速度下降。同时这一温升过程比较缓慢,所以在整个蚀刻过程中蚀刻速度变化不大。
(4)搅拌对蚀刻速度的影响:静止蚀刻的速度和蚀刻质量都是比较差的。这是因为在蚀刻过程中,一方面被蚀刻铜表面和蚀刻液中都会有沉淀生成,影响了铜的正常蚀刻;另一方面,铜在蚀刻过程中,被蚀刻表面的溶液会逐渐呈现暗绿色,这表明在补被蚀刻表面的FeCL3已跟铜表面发生了还原反应而失去了氧化能力。
cu+FecI,一cucl十Fe~:1
Cucl离子具有还原性,和腐蚀液叶J的Fe¨进一步反应生成cucl,。
Cucl+FeCl、一Cucl2+FeCl 2
生成的Cucl2具有氧化性,同样会与铜发生氧化还原反应。
Cu+c∞12——2cucl (5—43)
FeCl3
金属蚀刻原理结论:
FeC:l,金属蚀刻液是依靠Fecl,和cucl:同时完成的。其中n¨的氧化能力强,蚀刻速度快,蚀刻质量好。相对而言,CucI2在这里蚀刻速度较世,蚀刻质量差,随着蚀刻液中Fe3的消耗和cuCL2的增大而使蚀刻速度逐渐减慢,并使蚀刻质量恶化。当Fe3消耗量达50%时,蚀刻速度及蚀刻质量都将不利于继续进行蚀刻过程.而应更换蚀刻液。
在实际生产中,表示金属蚀刻液的蚀刻效能不是片Fe3的消耗量来衡量,而是采用蚀刻液中铜的溶解量(单位为昏g/l)来衡量。铜在FeCl3蚀刻溶液中,最初蚀刻速度是恒定的。然而,随着蚀刻液中Fe¨的消耗,蚀刻液中铜含量不断升高,当溶铜量达到60g/L时,蚀刻速度会变慢,当蚀刻液中Fe3消耗达到40%时或溶铜量达到83g/L时,蚀刻速度会急剧下降,此时的蚀刻液不能再继续使用,而应考虑蚀刻液的再生或更新。
通常使用的FeCl 3蚀刻液酸度都不高,所以FecL3蚀刻液在蚀刻铜时,也伴有FeCl,和CuCI,的水解副反应:
Fecl,+3H:O—Fe(OH)3 J+3HCI
cucl2+2H20一cu(on)2 +2HC:l
生成的氯氧化物不稳定,受热易分解牛成相应的氧化物和水,这些氧化物一部分沉淀在蚀刻槽底部形成黄土样沉积物,一部分悬浮于蚀刻液中,对抗蚀层产生一定的破坏作用。
2Fe(OH),一Fe202+3H3O
cu(OH)2—cuO +H2O
FeCl3金属蚀刻
原理如需了解更多请联系:刘先生13534257051 ly@sz-ydf.com
金属蚀刻工艺的特点
1.目标性,所谓目标性就是通过某一工艺流程的全过程有一个明确的输出,或者说要达到某一特定的目的。对金属蚀刻而言,这个目的就是满足其设计图纸对产品的要求。更具体地说,这些要求包括产品的蚀刻尺寸要求、经蚀刻后的表面粗糙度要求等。
2.内在性,所谓内在性,是指一个工艺流程必须需要有其内在的特定内容,也可以说是内容的实在性。这些内容包含于工艺流程的每一个步骤中,以及参与这些步骤的所有操作者的行为过程。
3.整体性,所谓整体性,是指工艺流程至少要有两个或两个以上的工序组成。因为,作为流程而言的工艺流程不可能是由一个加工步骤来完成,同时一个加工步骤也无法在工艺流程中完成流转,至少要两个或两个以上的步骤及其相关活动才能建立起一个基本的结构或者关系,才能进行流转。对于金属蚀刻工艺流程而言,也是由多个工序、各工序的工艺参数、各工序规定的工具及其相关设备组合而成的一个完整的工艺规范统一体,并且相互之间是不可分割的。
金属蚀刻的曝光原理
首先将需蚀刻的图形通过光绘的方式转移至两张完全一致的胶片菲林上,或是通过光刻的方式转移至两张完全一致的玻璃菲林上。然后通过人工对位方式或机器对位方式将菲林对准。再将已涂布感光油墨或贴好感光干膜的钢片置于菲林中间,吸气后即可曝光。曝光时对应菲林黑色处的钢片未被感光,对应菲林白色处的钢片感光,钢片感光处的油墨或干膜发生聚合反应。最后经过显影机,钢片上被感光的油墨或干膜不被显影液溶化,而未感光的油墨或干膜在显影液被溶化去除,这样需蚀刻的图形通过曝光就转移到钢片上去了。
曝光是在紫外光照射下,光引发剂吸收光能分解成游离基,游离基再引发不聚合单体进行聚合交联反应,反应后形成不溶于稀碱溶液的体形大分子结构。曝光一般在自动面曝光机内进行,现在的曝光机根据光源的冷却方式不同分风冷和水冷两种。曝光成像质量除干膜光致抗蚀剂的性能外,光源的选择,曝光的时间(曝光量)的控制,照相底版的质量等都是影响曝光成像质量的重要因素。
当曝光不足时,由于单体聚合不彻底,在显影过程中,胶膜溶涨变软,线条不清晰,色泽暗淡,甚至脱胶,在蚀刻过程中膜起翘,渗镀,甚至脱落;当曝光过度时,会造成难于显影,胶膜发脆,留下残胶等弊病。曝光将产生图像线宽的偏差,过量的曝光会使图形线条变细,使产品的线条变粗。根据显影后干膜的光亮程度,图像是否清晰,图像线宽是否与原底片相符等来确定适当的曝光时间。
蚀刻加工前的滚涂保护油原理
使胶辊与钢轮平行靠紧,并匀速向内旋转,油墨从胶管喷至钢轮上,均匀调节胶辊与钢辊之间的紧密度,就可以控制粘附在胶辊上的油墨厚度与均匀度;钢片由输送带往前匀速推进,与胶辊适当接触,胶辊上的油墨就均匀的转印到钢片表面上。 在蚀刻的防蚀层制作中涂装技术应用较多,常用的涂装方法有丝印法、浸涂法、喷涂法、电泳涂装等。涂覆的防蚀层表面应均匀完整、无砂眼、白点等,如发现防蚀层有上述质量缺陷,且这些缺陷又在图文线条附近,特别是精细图文线条,应退除防蚀层重新涂覆。工件上喷涂的感光油墨干燥后,在进行曝光之前要进行质量检查。检查项目包括油墨表面无划伤、气孔,油墨的均滚涂匀性等,如达不到这个要求应将整个板面的油墨退掉重新滚涂。
*光阻与钢片的附着力是靠光阻膜顺着钢片表面流动达成。
*加热可降低光阻的粘度并增加流动性,压力可将流动状态的光阻挤入钢片表面。
金属蚀刻前的滚涂原理
贴膜时,先从膜上剥下聚乙烯薄膜,然后在加热加压的条件下将干致抗蚀层粘贴在不锈钢材料上面。干膜中的光致抗蚀层受热后变软,流动性增加,借助于热压辊的压力和光致抗蚀层中胶黏剂的作用完成贴膜过程。干膜光致抗蚀剂是20世纪70年初期发展起来的一种感光材料,至今已有多种产品用于要求不同的生产需要。干膜具有良好的工艺性能,优良的成像性和耐化学药品性能,在线路板制造、图文制作及精密零件的切割上都得到了非常广泛的应用。
金属蚀刻不可用于加工窄而深的凹槽
这是因为在金属化学蚀刻反应所产生的汽泡会集聚在防蚀层边缘的下面,而这些被堵在防蚀层下面的气泡事实上起了把金属表面与腐蚀剂隔开的作用。以致造成一种非常不规则的腐蚀,形成很不整齐的边缘,这对于深度较大的加是一件麻烦事。虽然一些性能不错的防蚀材料较软,易于使气泡排出,对于这种加工到一定深度后,即使采用机械搅拌的方法也不足以使用权防蚀层边缘的气泡完全排出,但当加工到一定深度后,即使采用机模搅拌的方法也不足以使防蚀层边缘的气泡完全排出。对于这种加工最有效的方法就是采用比较费时的手工方法把图形边缘的防蚀层修平。另一种可能的原因就是腐蚀液表面张力的作用,这种情况同样也会在窄或小半径的表面造成腐蚀不能的情况,对于深度罗大的凹槽加工要求宽度不低于4mm,对于深度不大的凹槽或圆孔要求宽度或半径不小于深度的1.5倍。
蚀刻加工中的酸碱对工作人员的危害及救治
1、盐酸对工作人员的危害及救治
高浓度的盐酸对鼻黏膜和结膜有刺激作用,会出现角膜浑浊、嘶哑、窒息感、胸痛、鼻炎、咳嗽、有时痰中带血。盐酸雾可导致眼睑部能皮肤剧烈疼痛。如发生事故,应立即将受伤者移到新鲜空气处输氧,清洗眼睛和鼻,并用2%的苏打水漱口。浓盐酸溅到皮肤上,应立即用大量的清水冲洗5-10min,在烧伤的表面涂上苏打浆。严重者应立即送医院治疗。盐酸在空气中最高的容许浓度为5mg/m3
2、H3PO4对工作人员的危害及救治
H3PO4蒸气能引起鼻黏膜萎缩,对皮肤有相当强的腐蚀作用,能引起皮肤炎症疾患及肌肉损伤,甚至造成全身中毒现象。H3PO4在空气中最高容许量为1mg/m3。在工作中如不慎接触皮肤,应立即用大量的清水冲洗,把H3PO4洗尽后,一般可以用红汞或龙胆紫溶液涂抹于患处,严重时应送医院治疗。
3、常用金属蚀刻的材料不锈钢SUS304 SUS301 机械性能介绍:针对蚀刻工艺而言,SUS304材质性能更适合于蚀刻加工,SUS301的性能偏硬,蚀刻会有毛边,孔壁不光滑等缺陷。
金属蚀刻方式的选择
金属蚀刻的方式根据工件于溶液的接触形式主要有两种,即喷淋式蚀刻和侵泡式蚀刻。蚀刻方式的选择的原则有以下两种。
1.生产量:喷淋式蚀刻效率高、速度快、精度高,适合于有一定批量的生产,生产易于实现自动化控制,但是设备投入大,同时也不适宜对异形工件及大型工件的蚀刻;侵泡式蚀刻设备投入小,蚀刻方便,使用工件范围广。
2.工件形状及大小:对于大型工件由于受设备限制,采用喷淋式蚀刻难于进行,而侵泡式就不会受工件大小的影响。工件形状复杂,在喷淋时有些部位会出现喷淋不到位的情况而影响蚀刻的正常进行,而侵泡式由于是将工件整个侵泡在蚀刻液中,只要保持溶液和工件之间的动态,就能保证异性工件的各个部位都能充满蚀刻液并进行新液与旧液的连续更换,使蚀刻能正常进行。
对于不大的平面或近乎平面的工件如果条件允许,采用喷淋式蚀刻不管是效率或是精度都优于侵泡式蚀刻。所以,对于批量大、工件大小适中、形状简单的平面形状的工件以采用喷淋式为首选;如果工件外形较大,难以采用蚀刻机,工件形状复杂,批量不大,这式以采用侵泡式为宜。
金属蚀刻工件的后处理问题
蚀刻工件的保护膜去除之后,就显露出光泽的金属本色,例如:黄铜装饰件、铭牌、未蚀刻到的凸处是光亮的金黄色。被蚀刻到的凹处则是亚光或是无光的,层次清晰,经漂洗钝化后,表面罩上保护漆,即为成品。也有在被蚀刻到的凹处填上各种色漆,形成彩色的图案再罩上保护漆。高档工艺品脱膜后往往还要电镀,镀合金或真金或白银,再填漆罩光或直接罩光。也有局部电镀的,例如:不去除保护膜,在被蚀刻的部位镀上其它颜色,然后再去除保护膜,这样就是金银二色的产品了。显得精致、华丽,高贵。罩光的用保护漆以前有人用自干漆,当时好看但不耐久,现在多用烘干型涂料,紫光光(UV)固化涂料或电泳涂料。工业产品中使用不锈钢材质的零件,通常去除保护膜,清洗干净就好了,当然,有特殊要求的也可能需要表面着色,钝化或涂层。
金属蚀刻加工过程中的环境问题
金属蚀刻加工过程中影响的因素主要是酸、碱和三氯化铁,对其废涂必须妥善处理,不可随便排放。对于酸、碱废水一般都是用中和的方法进行处理,正好在蚀刻加工过程中有碱性废水,也有酸性废水,它们可以相互中和,当然不可能正好酸碱平衡,这就要检测PH值,缺啥补啥,使PH值达到排放的要求,同时还要清除过量的金属离子,经沉淀后,清水方可排放。三氯化铁废液对环境的污染,主要是其形象,沾到哪里,哪里就是一片黄锈,非常难看,损害环境。其废涂应罐装好由专业的加工单位回收。对含三氯化铁废水的处理,最普遍的处理方法是投入石灰乳,它不仅能驿酸起中和作用,还对废水中的三价铁及其它金属离子有沉淀作用,并对废水中的杂质有凝聚作用。
蚀刻加工前除油的作用
除油的目的是除去金属表面的油垢,作为需要金属蚀刻的工作不管是加工线路板或是加工一般的机械零部件还是装饰性工件,也不管是加工航天航空部件或是舰船等高要求工件。在这些待加工的工件中,有些是要进行图文蚀刻,有些是要进行结构蚀刻,有些只对其工件的一面或双面进行整体化学蚀刻。对这些工件的表面首先都必须要进行有效的清洁处理。一个理想的清洁表面必须是除了油脂、防锈层、氧化皮,同时又洗去了各种标记符号和其他不溶性外来物质的表面。这一清洁作用的目的是为了保证防蚀层在金属表面的粘附力和蚀刻速率均匀一致所不可缺少的条件。
蚀刻加工过程中水洗的作用
水洗在金属蚀刻的整个工艺流程中是采用得做多的一个步骤,每经过一次处理其后都要进行水洗。水洗的目的:1.要洗掉从碱性或酸性溶液中取出的工件表面所附着的碱性或酸性液膜代之以清洁的水膜,从而成为清洁的表面;2.工件从一个工序转移到下一个工序时,不至于将上一个工序的溶液带到下一个工序的溶液中。所以,水洗在金属蚀刻的圈过程中是左右其产品质量的重要过程。
金属蚀刻过程的控制
金属蚀刻质量的保证主要来自于对蚀刻过程的控制,金属蚀刻过程的控制分为化学参数控制和物理参数控制。
1.化学参数控制
化学参数控制对于维持蚀刻液均匀的蚀刻速度是非常关键的,化学参数控制主要包括溶液浓度的控制和溶液中各组分之间的比例控制。对这两方面的控制,前者的浓度控制容易,可以通过分析的方法就能确定溶液中成分的消耗情況。而对于后者控制难度要大一些主要是因为蚀刻液中的添加物质含量较低,并且可能是一些较难分析的材料,或和蚀刻液中的主料分离较为困难。
化学参数控制的依据来源于对溶液成分的分析而不是经验的估计,当然对于一些小厂并不排除操作者可以通过观察蚀刻过程进行的激烈程度、被蚀刻金属表面的状态以及溶液颜色的变化再根据经验来进行调节,并满足在一定程度上的可控性。这种方式对于成分单一的蚀刻液具有一定的实用性,但对于成分组成复杂,同时对金属蚀刻深度均一性要求较高的工件,采用这种方法有很大的局限性,难于保证批量生产的需要。从保证产品质量稳定的角度出发,要求蚀刻厂能把分析结果作为调整蚀刻液的依据。
化学蚀刻溶液的分析周期主要受以下几方面因素的影响:①溶液体积;②溶液的初始浓度;③单位体积的负荷量;④蚀刻量(一般以日为单位)。对这几方面的影响因素很容易理解,溶液体积小、溶液初始浓度低、单位体积的负荷量较大的情况下,蚀刻液成分的变化速度就快其分析周期就较短,反之则长。通常而言,如果蚀刻溶液体积不大,批量生产的情况下应保持每个班次分析一次(这里的班次是以8h为一个生产周期计算)。
2.物理参数控制
物理参数的控制分为通用参数控制及蚀刻方式所决定的其他参数控制。通用参数控制主要是对在蚀刻过程中时间、温度进行控制:由蚀刻方式所决定的其他参数控制包括浸泡蚀刻的溶液搅拌程度的控制以及喷射蚀刻的喷射压力的控制。在化学参数可控范围内,物理参数的控制对于维持其蚀刻速度的恒定及蚀刻均匀性是非常重要的。物理参数的控制相对于化学参数的控制来说要容易得多,也直观得多。同时,一些设备对温度、时间及喷射压力都有自控装置,只需要预先将这些参数输人即可。
任何金属蚀刻都一定有两个需要控制的指标,即深度和表面平滑度。虽然物理因素和化学因素的变化都会对蚀刻深度及表面平滑度产生影响,但在确定的蚀刻液成分及浓度的情况下,对深度的影响主要是物理因素,在温度、压力恒定的前提下,确保蚀刻深度指标的因素是蚀刻时间,在实际生产中也是通过时间来对蚀刻深度进行控制。而对于表面平滑度,虽然温度的变化会有一定的影响,但主要还是受蚀刻液的化学组分的影响,在化学组中添加物质对表面平滑度的影响比蚀刻主剂的影响更大,同时调整也更困难,但可以通过实验确定一个单位面积消耗量的经验值来控制。
地址:深圳市宝安区福永街道塘尾和沙路27号
直线:刘先生135 3425 7051(同微信) 邮箱:ly@sz-ydf.com
QQ刘先生:252292527;阿里旺旺-刘先生 :xieliuliu
公司网址:www.sz-ydf.com
生产线地址:东莞市虎门镇南栅社区第四工业区农林路1-3号银峰工业园C栋3楼
